3D printing of edible parts based on natural biopolymers opens up new prospects for pharmaceutical applications to obtain customized structures with targeted release kinetics of active ingredients. Adhesion between deposited layers requires the spreading of biopolymer filaments and the diffusion of macromolecules at their interface. This phenomenon is controlled by the surface tension of the molten biopolymer and its viscosity. To determine the printing conditions for different materials, their adhesion kinetics were characterized in situ under isothermal conditions, using X-ray micro-tomography on the ANATOMIX beamline.
The emergence of Additive Manufacturing by Material Extrusion (AM-ME) offers the opportunity to produce custom parts to control the release of active substances. However, the development of edible, absorbable materials remains a challenge, and some natural biopolymers appear to be an answer. Among them, zein, a corn protein, can be processed in the molten state, once plasticized with glycerol and an Active Pharmaceutical Ingredient - Ionic Liquid (API-IL), such as Lidocaine-Ibuprofen, combining local anesthetic and anti-inflammatory actions respectively.
The thermomechanical properties of this biopolymer have been studied, but its fusion-adhesion abilities need to be measured in order to determine its suitability for 3D printing. To this end, an instrumented oven was designed to monitor in situ the viscous sintering of two juxtaposed filaments using X-ray micro-tomography at the SOLEIL Synchrotron on the ANATOMIX beamline, for temperatures ranging from 100 to 140 °C (Fig.1-a). The two extruded zein-based filaments are placed side by side on a flat aluminum support. Once the set temperature has been reached, the suspended oven is lowered around the sample holder, allowing a controlled rotation of the filaments and the acquisition of 3D tomography volume data during sintering, while the oven is not rotating.

Figure 1:
a) instrumented oven.
b) Reconstructed image of a 3D scan of two juxtaposed plasticized zein-based filaments (⌀Filament=2mm, LFilament=5mm) and determination of the bonding angle θ=asin(x/r) according to a median vertical section.
The high intensity of the X rays from the synchrotron source and the cutting-edge equipment of the beamline made it possible to obtain a full 3D scan (consisting of 1000 individual projection radiographs) within only 1.2 seconds, at a resolution of 5.2 µm (pixel size). Scans were taken every 6 seconds.
Two types of zein-based filaments were extruded before the measurements to perform these tests: (i) zein plasticized by 20w% glycerol added as sole plasticizer (material A); (ii) zein plasticized by 10w% glycerol and 10w% API-IL, to target therapeutic properties (material B). Viscous sintering between the filaments is measured by determining the bonding angle, θ [rad], with θ = asin(x/r) (Fig. 1 b).
Both compositions show accelerated viscous sintering kinetics with temperature increasing from 100 to 140 °C (Fig. 2). The rate is higher in the case of material A, plasticized by glycerol only, because it is less viscous than material B, co-plasticized by glycerol and API-IL. Co-plasticization by glycerol combined with API-IL (material B), for the same weight proportion of plasticizer added to zein, is thus less effective in reducing the viscosity of the molten biopolymer than the addition of glycerol alone (material A).
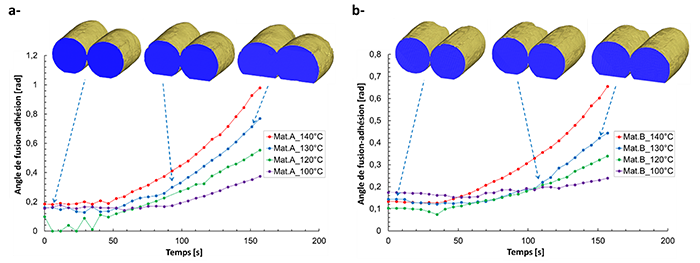
Figure 2: viscous sintering kinetics for different temperatures of two zein-based filaments plasticized by the addition of 20w% glycerol (material A, a-) and 10w% glycerol + 10w% API-IL (material B, b-).
The microtomography measurements on ANATOMIX have thus demonstrated the viscous sintering capabilities of thermoplastic zein-based materials. These materials enable the production of edible, resorbable 3D printed parts, particularly for high density with a rectilinear filling pattern favoring filaments bonding (Fig. 3). On the other hand, for parts with a more complex cellular structure, defects appear beyond 3 layers deposited for the co-plasticized composition (B), with lower sintering capacities.
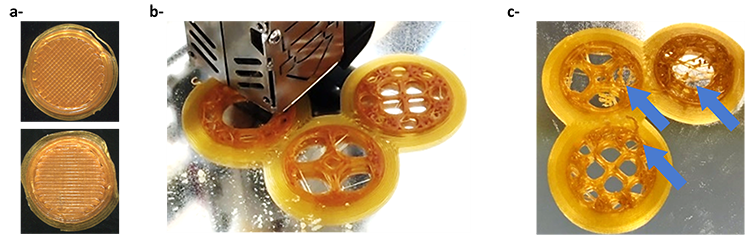
Figure 3: 3D-printed tablets at 130°C of zein plasticized with 20w% glycerol (material A, top) and 10w% glycerol + 10w% API-IL (material B, bottom) with ⌀Pellet=20mm (a-). 3D printing of complex zein-based parts: material A (b-) and material B (c-).
One of the prospects of this work is to understand the mechanisms of zein co-plasticization. Determining the adhesion properties of superimposed layers is also decisive for better control of printing parameters and improved design of digital models of parts with controlled porous structure.