Afin de pouvoir répondre aux besoins des expériences de diffraction de rayons X en temps résolu de type pompe-sonde-sonde, telles que celles réalisées sur la ligne de lumière CRISTAL, le groupe Détecteurs du Synchrotron SOLEIL a lancé un projet de R&D en 2017. Mené en collaboration avec la faculté AGH-UST de Cracovie (Pologne) qui a fourni les circuits microélectroniques intégrés permettant la lecture et le traitement du signal, ce projet consiste à concevoir un nouveau détecteur rapide à comptage de photons et résolu temporellement.
Ce détecteur utilise la technologie bien connue des pixels hybrides. Le détecteur se présente sous forme de plusieurs modules de matrices de pixels. Chaque pixel fait 75 µm de côté. Les pixels hybrides, qui sont des objets de haute technologie, ont la particularité d’être composés de 2 circuits micro-électroniques, empilés comme un sandwich, et interconnectés entre eux (voir illustration du concept en Figure 1).
Si les tout premiers modules de pixels hybrides ont été fournis par les collaborateurs de la faculté AGH-UST, et implémentés sur un détecteur prototype carré de taille de 2×2 cm2 [Reference 1], il était indispensable que le groupe Détecteurs du Synchrotron SOLEIL puisse également concevoir et faire produire ses propres modules de pixels hybrides, de différente taille et géométrie, afin de répondre de manière adaptée aux besoins spécifiques de SOLEIL.
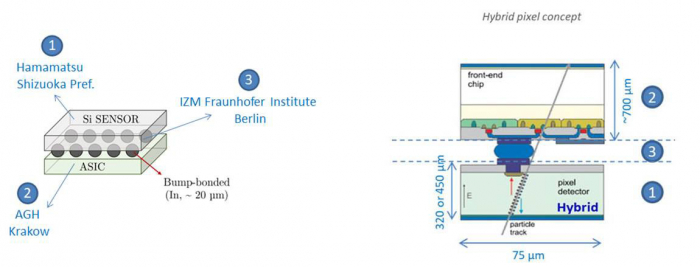
Figure 1 : Concept de pixel hybride et des différents intervenants dans le processus de fabrication
Pour pouvoir arriver au résultat final, il y a une multitude d’étapes complexes à accomplir :
1. Couche sensible pour la détection des photons
Il s’agit de concevoir la couche sensible au rayonnement des photons. Afin d’optimiser les coûts de fabrication, nous avons conçu plusieurs géométries et tailles de matrices de pixels sur la même galette de Silicium (appelée « wafer ») comme le montre la photographie de la Figure 2. Les pixels sont de type « P-on-N », ce qui signifie que la collection des charges, créées par l’interaction des photons, se fait par diffusion et dérive des trous dans le Silicium dopé N jusqu’à l’électrode (pixel) de type P (grâce à l’application d’une haute tension). La société Hamamatsu (Japon), spécialiste de galette de Silicium pour ce type d’application à façon, a finalisé les fichiers de fabrication suivant nos spécifications et nos échanges techniques. Une fois réalisées et inspectées en salle blanche à SOLEIL, les galettes de Silicium (qui comportent donc potentiellement plusieurs futurs détecteurs) ont été envoyées à l’institut IZM-Fraunhofer (Allemagne), spécialiste de fabrication de modules de pixels hybrides.
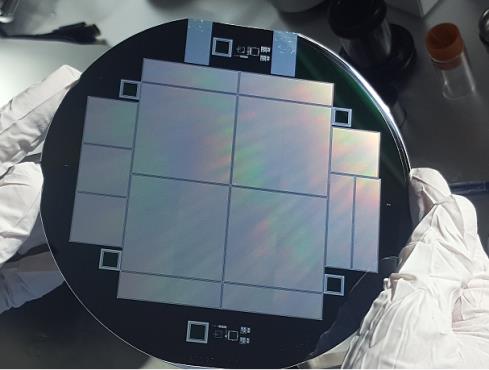
Figure 2 : Galette de Silicium comportant plusieurs géométries de modules de pixels hybrides pour les futurs détecteurs
2. Couche de lecture et de traitement du signal
Il s’agit de concevoir la couche de puces micro-électroniques (appelées aussi ASIC) qui ont pour fonction la lecture et le traitement du signal collecté venant de la couche précédente. Cette conception a été faite par le groupe de micro-électronique de la faculté AGH de Cracovie (Pologne). La réalisation a été faite chez un fondeur confidentiel et approprié, avec un choix technologique submicronique bien précis. De la même manière que dans l’étape 1, ces puces de lecture se présentent également sous forme de grande galette d’une centaine de puces. Après tests et sélection des meilleures puces (classées A, B, C, et D), cette grande galette a également été envoyée à l’institut IZM-Fraunhofer (Allemagne).
3. Interconnexion des pixels hybrides (étape « Bump bonding »)
Lors de cette étape cruciale et délicate, il s’agit de :
- découper soigneusement chaque puce de la couche de détection de la première galette,
- découper les puces sélectionnées de la deuxième galette,
- faire les couches de métallisation nécessaires à la connexion des puces entre elles,
- déposer les microbilles d’indium sur une des deux couches,
- aligner très précisément les puces du futur sandwich l’une au-dessus de l’autre,
- appliquer une pression pour refermer et chauffer doucement pour connecter le sandwich afin de former les modules de pixels hybrides.
Cette technique s’appelle l’interconnexion par « bump bonding ». La Figure 3 illustre un module rectangulaire finalisé de 65 536 pixels hybrides. Ce module est composé de 2 ASICs de lecture et d’un seul capteur Silicium (pas de zone morte pour la détection). Chaque module fabriqué est ensuite inspecté aux rayons X pour s’assurer que toutes les 65 536 connections sont bien présentes (pas de bille manquante, pas de craquelure, etc). Il est important de savoir qu’à cette étape, il n’est pas rare de casser et endommager un grand nombre de modules. Enfin, une fois les modules fabriqués, ils sont inspectés en salle blanche à SOLEIL, avant de les reporter définitivement sur leur carte électronique.
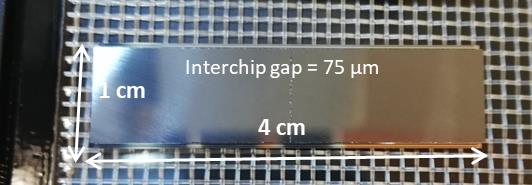
Figure 3 : Exemple de module rectangulaire de pixels hybrides après connexion par la technique de « bump-bonding »
4. Interconnexion des modules de pixels hybrides sur leur carte électronique (étape « Wire bonding »)
Les modules de pixels hybrides sont ensuite reportés définitivement sur leur carte électronique (circuit imprimé complexe), où ils sont connectés minutieusement par la technique de « wire bonding ». La connexion se fait donc pad-à-pad par des fils d’or ou d’aluminium de 18 ou 25 µm de diamètre. La Figure 4 montre une photo d’une partie zoomée du module de pixels hybrides avec les fils de « wire bonding ». Une fois encore, il n’est pas rare d’endommager de manière irréversible plusieurs modules lors de cette étape délicate.
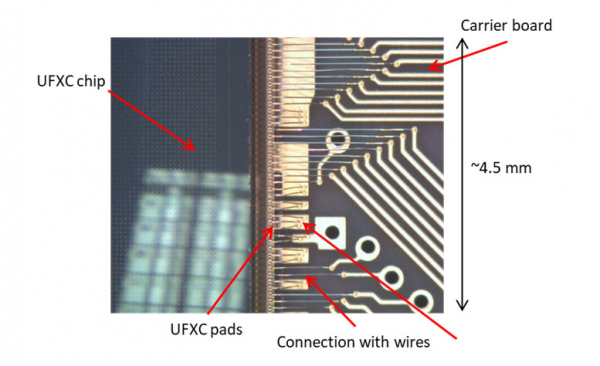
Figure 4 : Report et connexion par « wire bonding » d’un module de pixels hybrides sur son circuit électronique (zoom sur une partie seulement du module et du circuit électronique)
5. Tests de validation des assemblages complets avec des rayons X
Dernière étape du processus : il s’agit de tester le bon fonctionnement et les performances de nos modules de pixels hybrides fabriqués. Pour se faire, ils sont testés à l’aide du générateur de rayons X du groupe Détecteurs. La Figure 5 illustre un exemple d’image obtenue avec un faisceau de photons d’énergie E= 14 keV. Sur cette figure, le module de pixels est tout à fait fonctionnel, les pixels ont été calibrés, et le taux de pixels morts est très faible de l’ordre de 0.04%, ce qui est une très bonne valeur pour ce type de détecteur.
D’autres modules sont actuellement en cours de tests de validation, et seront montés prochainement avec leur mécanique et système d’acquisition pour en faire un détecteur complet prêt à l’usage.
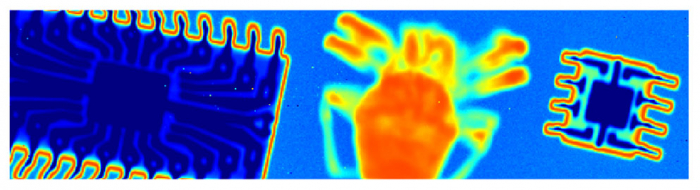
Figure 5 : Image obtenue avec le détecteur rectangulaire, illuminé par un faisceau de photons d’énergie E= 14 keV
En résumé, le groupe Détecteurs de SOLEIL a réalisé ses tout premiers modules de pixels hybrides avec succès. Ces modules sont des objets complexes, de haute technologie, qui ont impliqués 5 compagnies et 2 laboratoires de recherche (hors SOLEIL) pour une durée de conception, fabrication et tests de validation allant de 14 à 18 mois (en situation hors épidémie COVID).
Note : les premiers résultats expérimentaux ont été obtenus fin 2019 [Reference 2] sur la ligne de lumière CRISTAL (avec les premiers modules de pixels hybrides venant de la faculté d’AGH). Les nouveaux modules rectangulaires ‘made-in-Soleil’ ont été testés en Février 2021 sur la ligne ODE ; d’autres expériences sur ligne de lumière vont être planifiées prochainement avec cette géométrie particulière allongée. En parallèle, des modules hybrides de plus grande taille (avec 8 ASICs) ont également été fabriqués et seront testés prochainement.