Case study carried out with the start-up 3Dmagination
Improvements in the quality of X-ray beams, detectors and reconstruction algorithms, as well as the development of in situ sample environments enable the study of the micro-structure of materials subjected to extreme and evolving conditions (e.g. mechanical, thermal). This is performed non destructively using in situ microtomography with highspeed data acquisition. The observation and quantification of dendrite growth during the solidification of an Al-Cu alloy carried out in this study with 3Dmagination highlights the great potential of technique to address a wide range of industrial issues.
SOLEIL’s solution
The PSICHE beamline, dedicated to X-ray microtomography imaging and highpressure X-ray diffraction experiments, offers two modes: monochromatic (a single narrow bandwidth beam energy), providing maximum contrast or “pink” beam (with wide spectral bandwidth) for high-speed data acquisition (~1-10 seconds per scan). Equipped with a large hollow rotation stage allowing users to install sample environment equipment inside the stage (e.g. furnaces, compression cells, tensile testing machine) for in situ and real-time. Measurements of samples. The beamline also allows for further increased tomography data acquisition speed (< 1 second per scan) as well as variants in which tomography is combined with diffraction.
Solidification experiments have been carried out on a cylindrical sample (2.6 mm diameter) of an Aluminium-Copper alloy (~4% Cu) encased in a hollow alumina rod which was fixed to the tomography stage (for rotation and translation) and placed in a furnace allowing the passage of X-rays. After reaching its melting point (~660°C), the sample is slowly cooled at 5°C/min, down to 580°C. A series of tomograms were recorded, each lasting 5 s and containings 900 projections collected using a sCMOS Hamamatsu camera (FOV~2.6 mm x 2.6 mm) in pink beam mode every 30 s (30 scans in total), with a 1.3 μm pixel size.
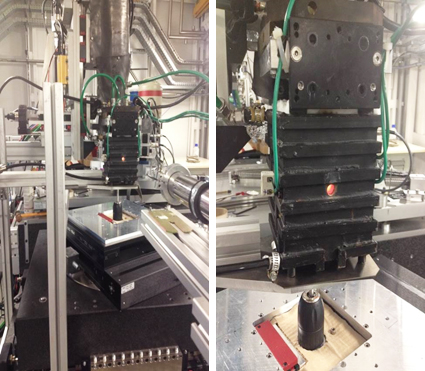
Experimental set-up: integration of the furnace* (operating in the 300-1500°C temperature range) on beamline PSICHÉ.
Results obtained
Dendrite coalescence appears to be the dominant mechanism for dendrite growth (figure 1). In contrast with the works of Limodin et al. 20091, the scientists did not observe any small dendrite arms re-merging for the benefit of larger arms by Ostwald mechanism, which is probably related to higher cooling speed. Special attention was given to the processing of tomographic data in order to extract local speeds in 3D for dendrite tips (Vtip). In fact, for a given undercooling, dendrite arms are expected to grow according to product Vtip x Rtip = constant (Gibbs et al., Sci Rep 20152; Daudin et al., Acta Mat 20163). Figure 2 shows that this relation seems to be verified in this experiment.
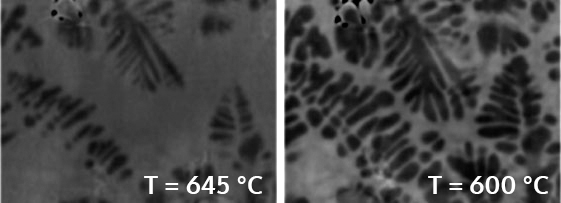
Fig. 1: 2D cross-sectional views extracted from volumes illustrating dendritic growth evolution in the course of solidification. Primary and secondary branches can be distinguished, surrounded by solute enriched liquid. The dendrite arms grow as solidification progresses.
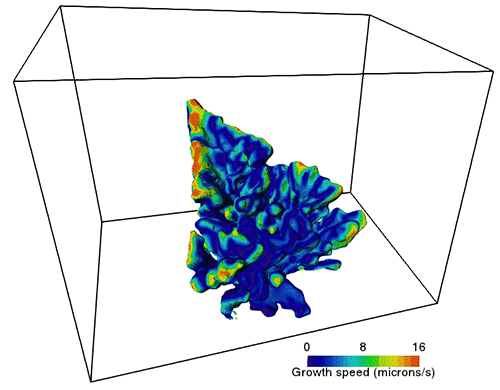
Fig. 2a: representation of the local speed determined from 3D surface meshes of solid-liquid interface in the course of solidification (local Euclidean distance between surfaces calculated and divided by the elapsed time between scans).
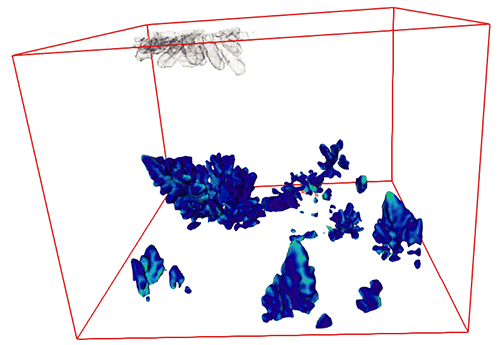
Fig. 2b: product of local speed by local curvature at the tip of dendrites.
Acknowledgments: Sylvain Gailliegue from Centre des Matériaux of MINES Paris Tech for the development and integration of the furnace*, Luc Salvo (Grenoble Institute of Technology) and Sofiane Terzi (ESRF, ESA, ILL) for their scientific advice on solidification and particularly Elodie Boller (ESRF) for the loan of the furnace*.